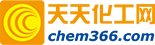
据中国汽车工业协会数据,2023年1-11月汽车产销分别完成2711.1万辆和2693.8万辆,同比分别增长10%和10.8%。其中新能源汽车产销分别完成842.6万辆和830.4万辆,同比分别增长34.5%和36.7%;新能源汽车新车销量达到汽车新车总销量的30.8%。新能源车的高速增长,对聚氨酯材料特别是聚氨酯胶黏剂的应用带来了一定的需求:
聚氨酯材料在汽车上一直具有广泛的应用,如车漆普遍使用耐黄变的HDI固化剂,座椅内部大量填充聚氨酯软泡,聚氨酯硬泡、半硬泡更是在门板、顶棚、仪表盘、遮阳板、翼子板等部件中广泛应用。
表1:聚氨酯产品在汽车上的应用
聚氨酯产品种类 |
用于汽车部件及零件名称 |
软质块状泡沫 |
遮阳板、车内四角装饰、车门内饰、隔音垫、空气滤清器、 密封垫及顶棚内衬 |
模塑泡沫塑料 |
座椅、坐垫、背靠、头枕 |
半硬质泡沫塑料 |
止推垫、柱状物、仅表箱、喇叭盖、扶手芯、遮阳板 |
整皮泡沫塑料 |
车门内衬及内装板、加工型内饰件 |
弹性RIM制品 |
保险杆、挡泥板、侧防护条、内饰件、仪表板、方向盘、大 灯壳、后灯 |
增强RIM制品 |
散热器板、阻流板、挡泥板、防护罩、行李箱、底板 |
浇注弹性体 |
减震缓冲块、手柄轴密封圈、滑块、轴承、方向节、门锁件 |
热塑性弹性体 |
弹性零件、齿条罩、车门部件、保险杆护板、顶衬、车窗件 、传送皮带 |
涂料 |
车漆固化剂,专门用于保险杆及其他外饰件涂装、动力电池壳体涂料 |
胶黏剂 |
见图1 |
但聚氨酯材料在汽车上的诸多应用之中,最广泛,遍及汽车几乎所有部件的,非聚氨酯胶黏剂莫属。
汽车的用胶场景包括玻璃粘连、动力电池、结构件和内饰粘接等。
图1:聚氨酯胶黏剂在汽车上的部分应用
若按用途划分,可以大致分为两类:
第一类为结构胶,即以结构粘接为主,兼顾一定的导热作用;既包括玻璃、结构件、内饰件、尾门等部件,也包括动力电池中电芯与电芯粘接、电芯与端板粘接、电芯与侧板粘接及电芯与箱体粘接。
第二类为导热胶,即以导热粘接为主,主要应用在动力电池上。导热胶应用的目的是将电芯工作时产生的热量导出到外部的散热部件,实现热管理的部分功能作用,兼顾结构粘接要求。
而在这两个方面,聚氨酯胶黏剂都有广泛应用。
结构胶:结构胶是指应用于受力结构件胶接场合,能承受较大动负荷、静负荷并能长期使用的胶粘剂。代替螺栓、铆钉或焊接等形式用来接合金属、塑料、玻璃、木材等的 结构部件,属于长时间经受大载荷、而性能仍可信赖的胶粘剂。车用结构胶最常使用的是丙烯酸胶、有机硅胶、聚氨酯胶和环氧胶。这几种叫胶各有优缺点,整体性能上环氧胶最优,具有较高的粘度且在工艺上更稳定。但环氧胶的抗冷热变化能力弱,受到冷热冲击后容易产生裂缝,导致水汽从裂缝中渗入到电子元器件内,防潮能力差;且韧性较聚氨酯胶差,且成本明显高于聚氨酯胶。聚氨酯胶具有较为优异的耐低温性能,韧性较好,并且具备较好的防水防潮、绝缘性。在车用胶黏剂中无论是整体性能还是价格都具有一定优势。
表2:主流车用胶黏剂性能对比
特性 |
环氧树脂 |
聚氨酯 |
有机硅 |
固化前 |
|||
固化速度 |
慢至快 |
慢至快 |
慢至快 |
温升 |
小 |
中 |
快 |
收缩性 |
高 |
中 |
小 |
固化后 |
|||
硬度 |
高硬 |
中硬 |
软 |
粘性 |
极好 |
非常好 |
一般 |
抗潮湿 |
很好 |
很好 |
很好 |
膨胀率 |
小 |
小 |
小 |
抗拉 |
中等到高 |
中等 |
低 |
剪切 |
中等到高 |
中等 |
低 |
延展性 |
低 |
中 |
高 |
绝缘性 |
好 |
很好 |
很好 |
耐老化 |
很好 |
很好 |
极好 |
导热胶:导热胶主要用于完成电芯与电芯之间,以及电芯与液冷管之间的热传导,胶的具体使用形式包括垫片、灌封、填充等。新能源汽车的电池模组与水冷板或车底座之间的粘接需要具备导热性能与粘接力。氨酯导热胶有高导热性、高粘接性和良好的操作性能,对改善电池热管理、提高电池系统总成性能具有重要作用。
新能源汽车在结构胶和导热胶两个方面的需求都明显高于传统车,这主要归功于新能源汽车的心脏---动力电池。
电池包的结构从传统的CTM(Cell To Module,将电芯集成在模组上)加速向CTP(Cell to Pack,直接将电芯集成在电池包上)转变。CTP技术的核心点在于取消了模组设计,电芯直接与壳体相结合,减少了端板、隔板的使用,进一步压榨电池包内空间,有效提升了电池包的空间利用率和能量密度。CTP电池结构取消了电芯与模组连接固定的机械结构。目前主流的方法是采用钢带或胶带等把结构相对简单的方块电池进行固定,再把一大块电池通过导热结构胶粘接到液冷板上。
图2:CTP电池结构
除了CTM和CTP之外,动力电池包还有比亚迪为首的CTB()和特斯拉为首的CTC技术,这两种技术都是将电芯直接安装在底盘上。从这里就不难看出,无论是CTP还是CTB、CTC,都需要大量的结构胶、灌封胶来实现电芯在车辆高速运行和颠簸路况下始终保持稳定,更需要导热胶来将电芯的热量快速传导至冷却板。
目前,动力电池广泛使用双组份聚氨酯胶黏剂。并且在环氧树脂胶中,聚氨酯材料也常常充当固化剂、增韧剂。据估算,仅动力电池胶一项,平均每辆新能源汽车聚氨酯消费量就比传统燃油车高出**kg,部分使用了聚氨酯电池盖、聚氨酯动力电池壳体防火涂料、聚氨酯灌封泡沫/防冲击吸能泡沫等材料的新能源汽车,平均消费量甚至比普通燃油车高出**kg。双组份聚氨酯胶黏剂中大量使用MDI、TDI和聚醚多元醇。根据主流双组份聚氨酯配方估算,平均每辆新能源汽车TDI的单耗量约为**kg,MDI的单耗量约为**kg,聚醚多元醇的单耗量约为**kg。据此推算,2023年全年中国新能源汽车动力电池胶TDI消费量***kg,MDI消费量***kg,聚醚多元醇消费量***kg。
行业展望:中国是全球新能源汽车最大的生产国和消费市场,拥有全世界最完善的新能源汽车产业链,随着消费者对环保和节能的认识不断提高,以及政府对新能源汽车持续的扶持政策、后续技术进步带来的置换需求对汽车销量预计会形成持续支撑,中国新能源车市场规模有望持续保持高速增长。而聚氨酯材料特别是聚氨酯胶黏剂在新能源车上的应用也会愈发成熟、稳定、多样化,增量需求前景可观。
如您对2023年中国聚氨酯电池胶市场及其对TDI、MDI、聚醚多元醇消费感兴趣,
欢迎垂询和订阅:天天化工网《2023年亚太区TDI市场研究报告》。
天天化工网《2023年亚太区MDI市场研究报告》。
天天化工网《2023年亚太区PPG市场研究报告》。