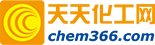
己二酸的生产工艺方法主要有 4 种方法,即苯酚法、丁二烯法、环己烷法和环己烯法。其中,苯酚法已基本被淘汰,而丁二烯法仍在开发研究中,现在主要是环己烷法和环己烯法。这两种工艺路线的原料均为苯、氢气和硝酸,主要区别在于中间产品不同,环已烷法的中间产品是环己醇和环己酮的混合物,而环己烯法的中间产品是环己醇,但后续的己二酸生产工艺基本上都是相同的。
环己烷法是目前世界上己二酸生产中主要采用的方法,其产量一度占到全球产量的主流,于 20 实际70 年代由美国杜邦公司开发,该工艺方法是以苯为原料,经加氢反应生成环己烷,环己烷和空气反应制取环己醇和环己酮的混合物(即醇酮油,简称 KA 油),KA 油经硝酸氧化生成己二酸。
环己烯法(也称环己醇法)是20世纪80年代由日本旭化成公司新开发的工艺路线。此法是以苯和氢气为原料,控制一定的温度和压力,在钌基催化剂作用下对苯进行部分加氢生成环己烯,然后经水合生成环己醇,通过精馏得到精制环己醇,最后再与硝酸氧化生成已二酸。
图一,两种生产工艺比较
相较于国外绝大多数己二酸由环己烷法生产,我国己二酸行业近几年环己烯法生产装置显著增加,且占比较大。截止至今,我国的环己烯法产能占国内有效产能的59%。环己烯法产能的迅速增长主要得益于其高采收率,更高的产品质量以及规模扩张之后更低的原材料单耗与能耗,以及副产物的利用更为简单,因此其大规模装置与环己烷法相比,其成本更低。
图二,主要生产企业原料生产工艺及原料来源
图三,两种工艺制己二酸单耗比较
从上表可以看到,与环己烷法相比,环己烯法在苯的单耗上减少了 0.046 吨,氢气消耗大幅降低,节省 40%以上。此外,环己烷法的副产物成分复杂,难以利用,而环己烯法的副产物主要为环己烷,环己烷可以经硝酸氧化再生产己二酸,或直接对外出售,进一步降低了成本。